Detachable plate heat exchanger
Our FLFA traditional plate heat exchangers are ideal for a wide range of applications in a wide range of markets. We have a wide range of plate types, we customize each heat exchanger to meet your exact requirements. Innovative technology and intelligent design make our traditional plate heat exchanger an excellent investment.
Product description
Traditional detachable plate heat exchanger
The reliable quality and high thermal efficiency of our FLFA traditional plate heat exchangers make them a widely used solution.
What does this mean for you?
We work closely with our customers to develop plate heat exchangers. Because we understand the processes behind the production process, each solution is customized and configured to suit you and your business.
Our extensive portfolio and mode options ensure that we always have a solution that works well for you. Our model creates the ideal turbulent flow and takes advantage of the available pressure drop.
Always effective choice
We design single-channel solutions where possible because they are suitable for most applications. On all connections to the head, you do not need to disconnect the heat exchanger of the pipe to perform inspections, cleaning or service. Quick and easy installation and maintenance using FLFA heat exchangers.
With the smallest possible space requirements, low energy consumption, and reduced sheet count required for high performance, FLFA heat exchangers are designed for tomorrow's design.
Features and benefits
Experience the benefits of a single, customized solution that exactly matches your needs and reduces your energy consumption.
The high performance and low pressure reduction eliminates the unnecessary burden of the system and optimizes the performance of the entire system.
The result of this design is a compact solution with minimal footprint, easy installation and easy maintenance.
Basic structure
The heat conducting plate is formed by stamping with corrosion-resistant stainless steel or titanium. A gasket is placed on each plate. The plates are suspended from the guides and bolted together between a mounting bracket and a movable frame. A fixed gap between the plates allows the liquid to flow sufficiently. The inlet and outlet fittings can be mounted on a mounting or moving frame.
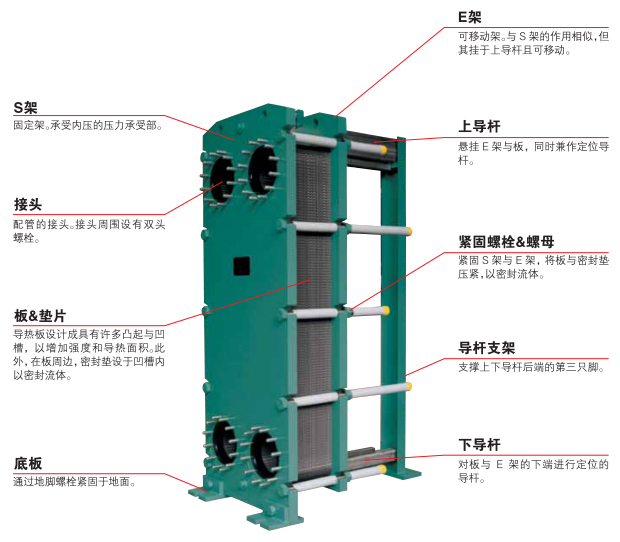
Flow channel
The heat conducting plates are divided into A plates and B plates, and a passage is formed between the plates. The cryogenic liquid of the high temperature liquid alternately flows in the opposite direction for heat exchange. Thus, high thermal conductivity is obtained by these sheets. When the A board is inverted, it can be used as a B board. Therefore, for many series, only one type of board can be used as the A board or the B board.
Thermal plate
Each heat conducting plate is machined into various corrugated shapes to enhance its strength and thermal conductivity. In addition, corrugations can increase turbulence to increase thermal conductivity. The heat conducting plate has a passage hole at each corner. Each plate is sealed with a gasket that fits into its outer edge groove.
Channel design
In the single-channel design, all joints are only placed on one side of the holder, making piping easier and more flexible. In the multi-channel design, the joint is installed on both sides of the S frame (fixed frame) and the E frame (movable frame), so the pipe needs to be removed and adjusted.
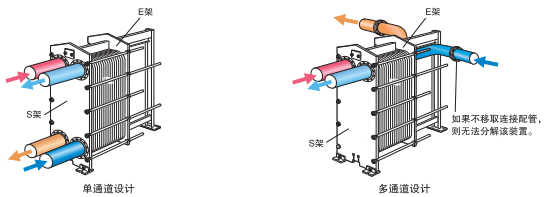
Wide range of standard models
Capacity range: 0.1m3/h to 5000m3/h
Operating pressure: up to 3.0MPaG
Operating temperature: up to 180 ° C
Surface area: 0.18m2 / set ~ 2500m2 / set
Board material:
Stainless steel: 304SS, 316SS, 316LSS, 317LSS and others
Titanium: Ti, Pd-Ti
Nickel base and gold: C-276, C-22, B, G and others
Nickel: Ni
Other materials: in line with relevant international standards
Gasket materials: NBR, EPDM, RFPM silicon, TCG, etc.
High performance
Since the corrugations on the plates provide high turbulence, the overall thermal conductivity (U-value) can vary from 4000 to 9000 W/(m2·°C) in water-water heat exchange. This is one of the reasons why plate heat exchangers have a high thermal conductivity. In addition, this high turbulence prevents scale formation on the surface of the board.
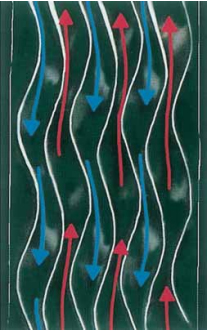
The effective use of temperature difference between import and export reaches its limit
The structure of the plate heat exchanger enables heat exchange with a very high thermal conductivity. Therefore, in complete countercurrent, the heat exchange only needs to utilize a temperature difference of 1 ° C or less.
Prevention of internal mixing of liquids
Specially considered gaskets prevent it from being directly attacked by liquids. In addition, the gasket is double sealed to allow liquid to be discharged to the outside of the exchanger when the gasket is degraded to cause liquid leakage.
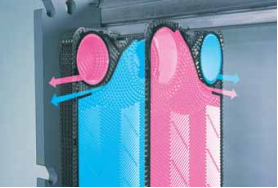
Heat transfer capacity and capacity are easily changed
Depending on the change in processing capacity, the heat transfer surface area can be increased or decreased by loosening the clamping bolts of the plate, increasing or decreasing the number of plates.
Steam can be used as a heat source
The use of special-purpose synthetic rubber gaskets allows steam to be used as a heat source, ie operating temperatures up to 180 °C.
Less installation area required
The lightweight and compact construction reduces the required installation space and weight to 1/4 and 1/3 of the multi-tube heat exchanger. In addition, light and thin heat-conducting plates are easy to install due to less liquid storage.
When cleaning, the board can be removed without separation from the main line, and the multi-tube type requires additional space for the removal of the tube.